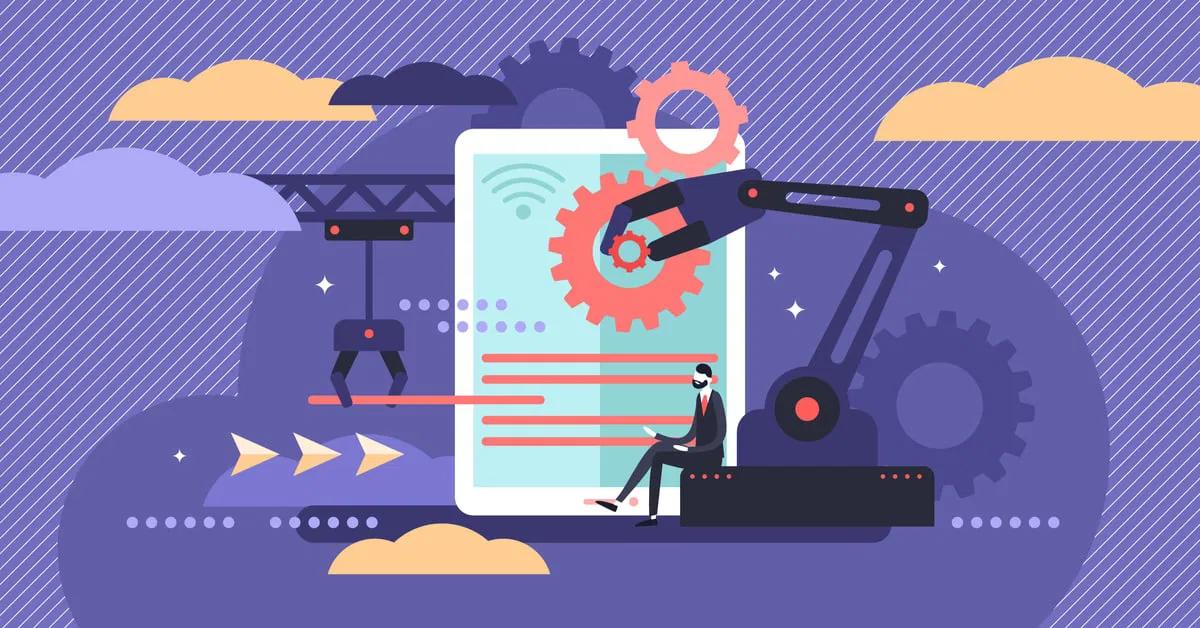
5 modi per minimizzare gli sprechi nella produzione manifatturiera
All’interno del workflow manifatturiero di una PMI esiste un’ampia casistica di sprechi che ogni addetto al reparto produzione deve cercare di ridurre il più possibile al fine di ottimizzare l’efficienza dell’azienda.
Quando chi si occupa del reparto produzione di una PMI manifatturiera legge la parola “sprechi”, la prima cosa a cui pensa, giustamente, sono gli scarti di lavorazione. In realtà il termine comprende anche tutta una serie di altri elementi e attività che spesso non si considerano e che impiegano risorse senza di contro conferire valore all’interno del sistema produttivo. Eccone qui di seguito i 5 tipi principali, per ciascuno dei quali esiste anche, come vedremo, una soluzione per ridurli:
1. Non conformità e inefficienza - Quando manca un controllo della Qualità, il reparto produttivo di un’azienda manifatturiera lavora a circa il 50% del proprio potenziale. Inoltre, anche produrre articoli non conformi genera sprechi, in quanto hanno dei costi, non possono essere rivenduti e richiedono delle rilavorazioni. Effettuare un’analisi costante e meticolosa del workflow non è però semplice e necessita di tempo e risorse, motivo per cui anche questa procedura può, paradossalmente, costituire uno spreco.
2. Scorte - L’accumulo in stock di scorte, siano esse materie prime, semilavorati o componenti di ricambio per la manutenzione dei macchinari, avviene solitamente in previsione di eventuali necessità dovute a inefficienze del sistema produttivo, come per esempio l’incapacità di calcolare gli approvvigionamenti necessari. Tale accumulo rappresenta uno spreco in termini di costi e di logistica, poiché non è dato sapere se e quando tutti quegli elementi già acquistati serviranno.
3. Stop produttivi e tempi morti - Qualunque pausa si verifichi all’interno del workflow rappresenta uno spreco. A risentirne non è solo la tempistica di realizzazione e di consegna ma anche la voce costi: ogni ritardo rappresenta infatti una perdita in termini di produttività e quindi di guadagno. Ecco perché macchine ferme in attesa degli operatori, materiali in attesa di lavorazione e così via sono veri e propri sprechi di efficienza e di potenziale.
4. Sovrapproduzione – All’interno dell’ingranaggio della produttività, ogni processo deve avere una causa e un fine ben precisi e identificati. Nel caso dei prodotti, questo significa che ciascuno di essi deve essere realizzato come risposta a una richiesta. Produrre in surplus significa impiegare tempo, risorse, operatori, macchine e materiali operando al di fuori del piano produzione, esponendosi per di più al rischio che l’ordine venga annullato o modificato.
5. Spostamenti – La stessa parola “workflow” (flusso di lavoro) suggerisce già da sola il concetto di spostamento: qualunque elemento interessato dal ciclo produttivo infatti subisce una dislocazione da un punto iniziale a uno finale. Spesso però un’errata disposizione di macchinari, magazzini e mezzi di trasporto genera all’interno del reparto produzione una caotica serie di spostamenti lunghi e inutili. Tutto questo rappresenta uno spreco di tempo e non conferisce valore aggiunto al prodotto e al servizio al cliente.
Queste 5 tipologie di sprechi possono essere minimizzate grazie alla digitalizzazione dei processi, ovvero tramite l’adozione di sistemi informatizzati all’interno del reparto produzione, connessi tra loro in rete e in grado di fornire, analizzare e condividere dati sul loro operato. Fondamentale diventa in questo caso l’adozione del giusto software gestionale ERP, in grado di offrire uno strumento unico con cui governare tutte le funzionalità del sistema, di accedere ai dati raccolti e di effettuare calcoli utili a ottimizzare la produttività in modo matematicamente preciso.
Con il giusto software gestionale, tarato sulle esigenze e sulle dimensioni dell’azienda, diviene possibile:
- Monitorare la Qualità in modo capillare lungo tutta la filiera e verificarla tramite una continua analisi dei dati produttivi. In questo modo l’efficienza viene misurata in modo oggettivo e l’incidenza degli sprechi viene quantificata e ridotta.
- Monitorare le code ed effettuare una programmazione a capacità finita, in modo da evitare l’accumulo di scorte ingombranti e costi inutili.
- Eliminare le attese, strutturando il flusso dei materiali in base al calcolo sincronizzato dei tempi di lavoro delle macchine e degli operatori.
- Schedulare con precisione gli ordini di produzione e coordinare gli approvvigionamenti e i vari reparti in modo da rispettare nel dettaglio ogni richiesta del cliente.
- Riorganizzare i singoli comparti in modo razionale, connettendoli in rete per una condivisione istantanea delle informazioni, in modo da limitare al minimo gli spostamenti e la movimentazione di materiali all’interno dell’area produttiva.
Il software gestionale andrebbe sempre scelto in base alla sua reattività e alla sua capacità di risposta alle esigenze dell’azienda, in modo da poter implementare subito i nuovi parametri produttivi e minimizzare gli sprechi.
Per avere un’idea delle potenzialità del giusto ERP, scopri anche tu il software gestionale SAP Business One usato da oltre 55.000 PMI nel mondo